Lehre
Lehrveranstaltungen
Lehrveranstaltungen Werkstoffkunde/ -technik bzw. Werkstoffe A/B in den Studiengängen Maschinenbau, Internationales Ingenieurwesen, Kooperatives sowie berufsbegleitendes Ingenieurstudium und Wirtschaftsingenieurwesen
Praktika
Zugversuch
Der Zugversuch gehört zu den zerstörenden Prüfverfahren und kann im Labor bei individuellen Prüfbedingungen durchgeführt werden. Hierzu gehören variable Belastungen (quasi-statische, ruhende und wechselnde Beanspruchungen), individuelle Temperaturen von -273°C bis 950°C und einstellbare Prüfgeschwindigkeiten.
Im Rahmen des Praktikums werden Zugversuche an unterschiedlichen Materialien durchgeführt. Aufgabe der Studierenden ist hierbei die Erstellung der zugehörigen Diagramme, die Zuordnung von Werkstoffen und die Ermittlung von Festigkeitskennwerten.
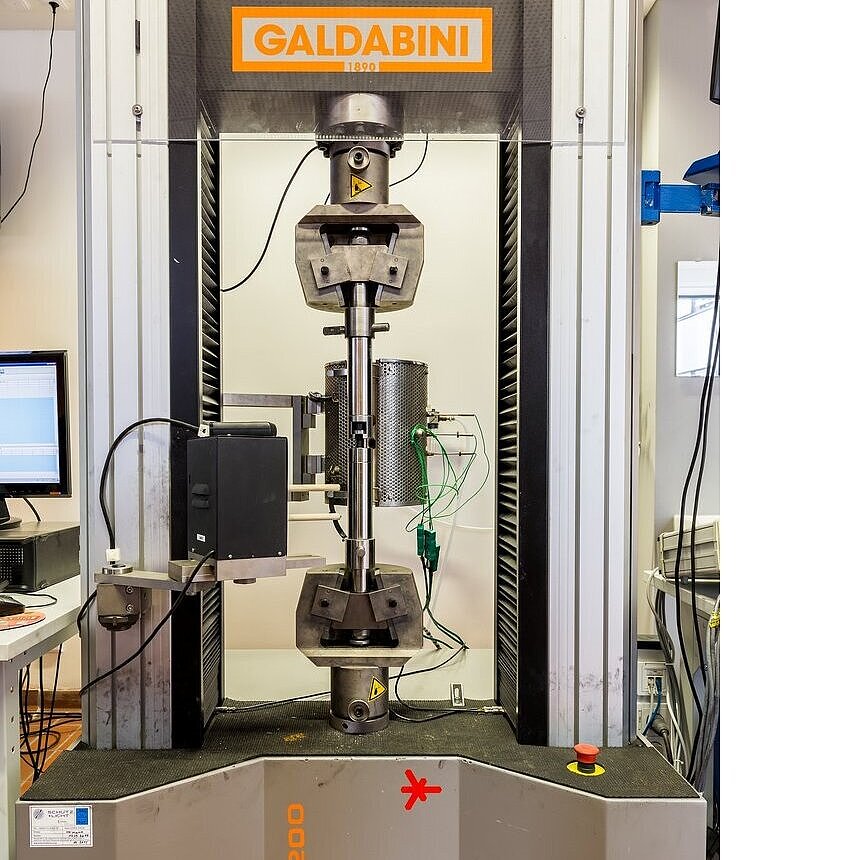
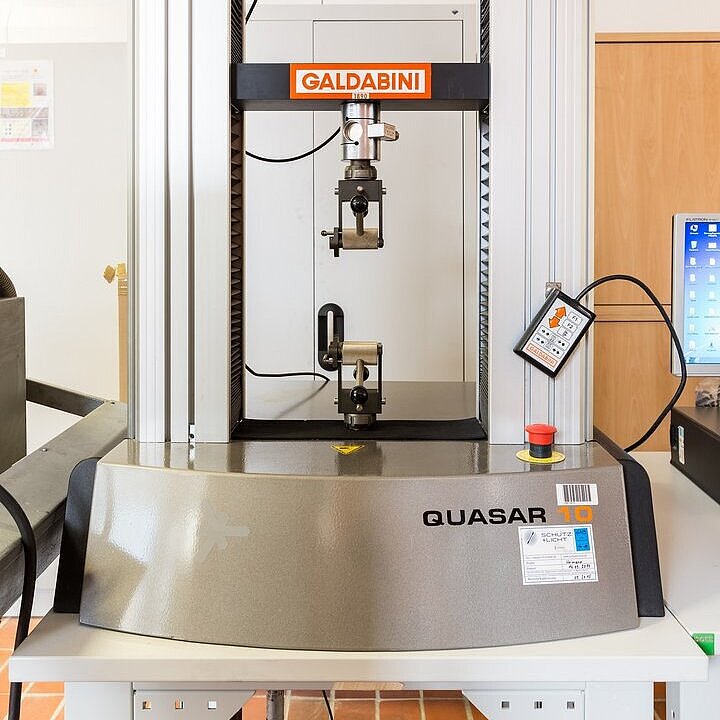
Härtemessung
Härte
Als Härte wird der Widerstand bezeichnet, den ein Werkstoff dem Eindringen eines Körpers entgegensetzt. Werkstoffe mit hohen Härtewerten sind meist spröde. Sie halten plastische Verformung folglich kaum aus und brechen unerwartet. Werkstoffe mit geringen Härtewerten nutzen sich bei Relativbewegung mit anderen Bauteilen schnell ab. Die Härte eines Werkstoffes kann folglich als Maß für das Verschleißverhalten herangezogen werden. Mithilfe von Tabellen können bestimmten Härtewerten Zugfestigkeiten zugeordnet werden. Diese stimmen näherungsweise mit den im Zugversuch ermittelten Werten überein.
Es gibt unterschiedliche Verfahren zur Bestimmung der Härte. Im Praktikum des WKP-Labors werden Härteprüfungen nach Vickers, Brinell und Rockwell demonstriert bzw. durchgeführt.
Kerbschlagbiegeversuch
Beim Kerbschlagbiegeversuch werden sogenannte Zähigkeitskennwerte ermittelt. Der Versuch wird mit Proben durchgeführt, die auf Temperaturen von ~150°C bis 200°C gebracht werden. Zähigkeitskennwerte sind aufgrund von Einflussgrößen wie Reinheit des Werkstoffes, Probenquerschnitt oder Kerbform nicht ohne Weiteres miteinander vergleichbar. Da bestimmte Werkstoffe bei speziellen Temperaturen verspröden und in der Praxis meist mehrachsige Belastungszustände vorliegen, ist dieser Versuch von großer Bedeutung.
Den Kerbschlagbiegeversuch führen die Studierenden selbstständig durch und berechnen aus Ihren Ergebnissen zugehörige Zähigkeitskennwerte. Sie werden außerdem an die Thematik herangeführt, Zähigkeiten anhand von Bruchbildern abzuschätzen.
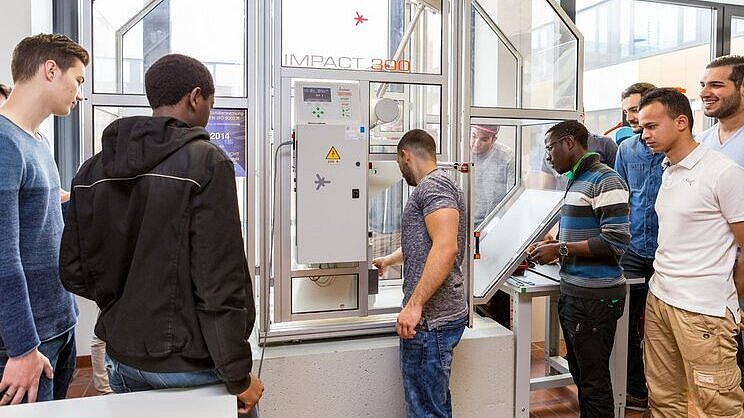
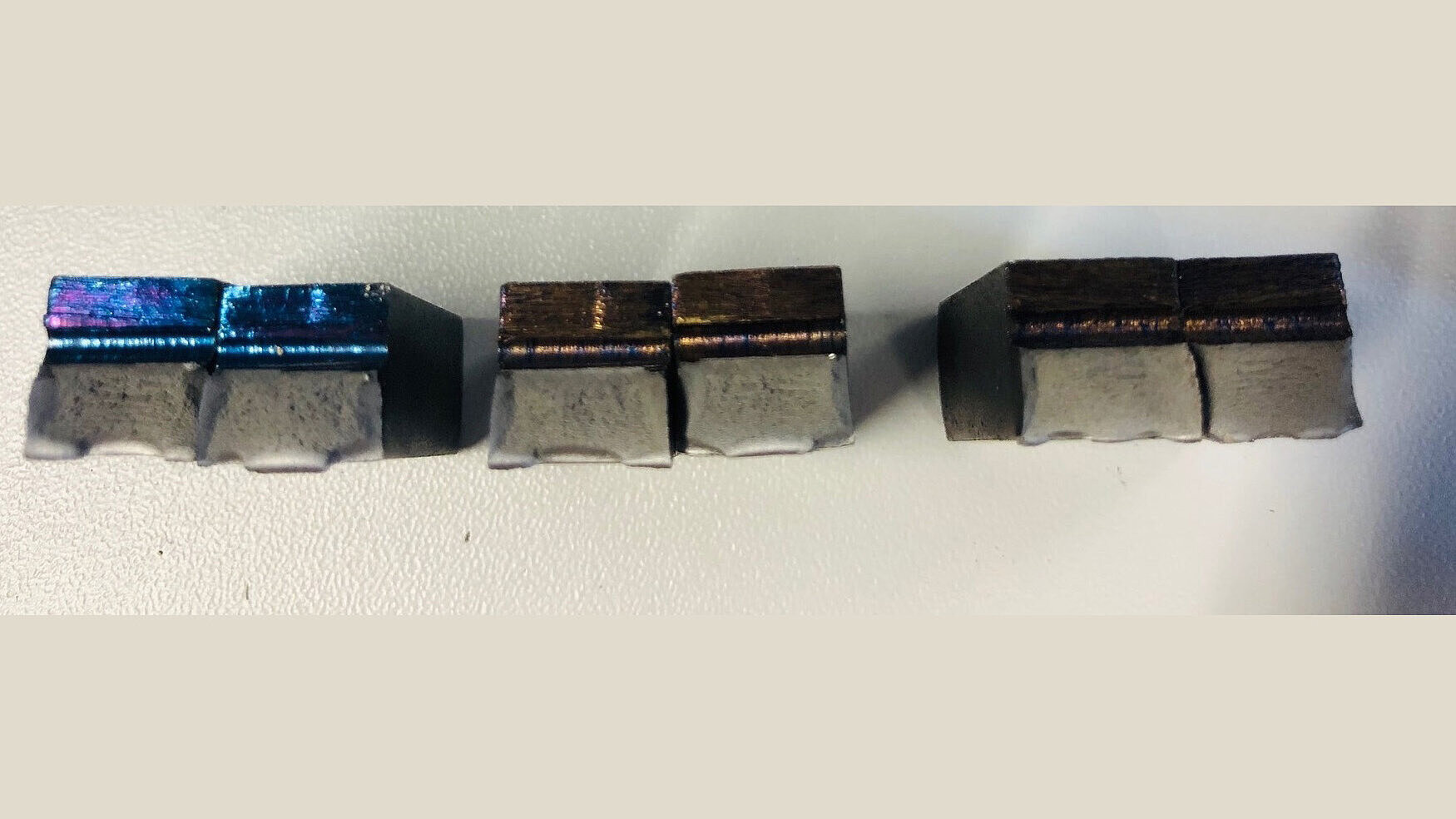
Lebensdauer
Schwingend belastete Bauteile brechen weit unter Streckgrenze. Grund dafür sind Ermüdungen des Werkstoffes. Ermüdungen sind plastische Verformungen die u. A. zum Auftreten von Rissen führen. Bei zyklischer Beanspruchung können diese winzig kleinen Risse dann so weit wachsen und durch das Bauteil wandern, bis die Spannungen im tragenden Querschnitt so hoch werden, dass das Bauteil bricht. Bauteile werden selten rein statisch beansprucht und trotzdem in der Konstruktionsphase nach Festigkeitskennwerten aus dem Zugversuch ausgelegt
Eine Option, Werkstoffe auf schwingende Belastung zu testen ist der Dauerschwingversuch. Mithilfe des Versuchs kann die sog. Dauerschwingfestigkeit ermittelt werden. Mithilfe von Wöhler Kurven kann die Lebensdauer von Bauteilen abgeschätzt werden.
Stirnabschreckversuch
Beim Härten klappt das kubisch-flächenzentrierte Gitter eines Stahls in ein raumzentriertes Gitter um. Hierdurch kann sich Kohlenstoff im Gitter einlagern. Wird schnell genug abgekühlt, so kann der Kohlenstoff nicht mehr hinaus diffundieren und sorgt für Eigenspannungen. Diese müssen nun beim Wandern von Versetzungen zusätzlich über-wunden werden. Folge daraus sind höhere Festigkeiten und sprödes Werkstoffverhalten.
Nachdem den Studierenden der Jominiy-Versuch demonstriert wird führen diese selbstständig Werkstoffprüfungen an unterschiedlichen Proben durch. Sie tasten sich eigenständig an die Fragestellung nach der Durchhärtbarkeit von Werkstoffen ran und lernen im zweiten Teil des Praktikums wie Werkstoffe, bei denen keine Gitterumwandlung stattfindet gehärtet werden können.
Auslagern von Aluminiumlegierungen
Aluminium ist ein Nichteisenmetall. An der Luft und in Wasser verbindet es sich mit Sauerstoff und bildet eine Oxidationsschicht. Diese ist gut korrosionsbeständig und stellt eine natürliche Schutzschicht für den Werkstoff dar. Die Dichte von Aluminium liegt mit rund 2,7 kg/dm³ weit unter der Dichte von Eisen/ Stählen mit rund 7,7 kg/dm³. Auch haben Stähle eine deutlich höhere Festigkeit als (Rein-)Aluminium. Jedoch lässt sich diese, sowie weitere mechanische Eigenschaften von Aluminium, durch die Zugabe von Legierungselementen wesentlich beeinflussen.
Aluminiumlegierungen lassen sich in aushärtbare und nicht aushärtbare Legierungen unterteilen. Während bei nicht aushärtbaren Legierungen Härte- und Festigkeitssteigerung durch Mischkristallbildung erreicht werden, müssen aushärtbare Legierungen wärmebehandelt werden. Hierbei lassen sich Festigkeitswerte erreichen, die denen der Stähle/ Eisen nahe kommen.
Prozess des Ausscheidungshärtens
Im Aluminiumkristall befinden sich Legierungselemente [LE] zunächst an den Korngrenzen. Während des Lösungsglühens unter ~ 500°C (+/- 20°C) entsteht ein Mischkristall, in dem sich alle Legierungselemente homogen lösen. Wird die Legierung in diesem Zustand rasch abgekühlt, so können die LE nicht aus dem Gitter diffundieren und verspannen das Gitter. Diese Spannungen sind jedoch so gering, dass hierdurch keine wesentlichen Härtesteigerungen erzielt werden können.
Aus diesem Grund werden Aluminiumlegierungen in einem weiteren Schritt ausgehärtet (auch: ausgelagert). Eingelagerte Legierungselemente erhalten durch die nachgestellte Wärmebehandlung Energie in Form von Wärme und können dadurch innerhalb des Kornes diffundieren. Diese Bereiche wachsen mit fortschreitender Auslagerungsdauer. Müssen nun Versetzungen durch den Werkstoff wandern, so stellen diese Ausscheidungen Hindernisse dar und bewirken dadurch Härte- und Festigkeitssteigerungen (= Ausscheidungshärten).
Studierende erhalten im Rahmen des Praktikums die Möglichkeit, den Aushärtungsprozess einer ausgewählten Aluminiumlegierung selbstständig herbeizuführen und zu dokumentieren. Sie erstellen unterschiedliche Härteverlaufskurven für unterschiedliche Auslagerungstemperaturen und lernen, aus welchem Grund Werkstoffe überlagert werden können.
Kerbwirkung
Veranschaulichung der Kerbwirkung anhand von Dehnmessstreifen an einer in der Länge rund gekerbten Probe
Innerhalb ungekerbter Proben verteilt sich die Spannung gleichmäßig über den gesamten Querschnitt. Ungleichmäßig wird die Spannung an allen Querschnittsänderungen verteilt: Kerben, Bohrungen, Nuten etc.. Die Kerbwirkung beschreibt folglich jede Querschnittsänderung eines Bauteils, die eine Änderung des Kraftflusses im Inneren zur Folge hat. Es entstehen sog. Spannungsspitzen.
Um die Kerbwirkung „sichtbar“ zu machen, kann ein Alu-Blech mit vier Dehnmessstreifen (DMS) versehen und anschließend in eine Zugprüfmaschine gespannt werden. Dehnmessstreifen sind Sensoren, deren Widerstand sich mit angelegter Kraft ändert. Liegt am Alu-Blech eine Tonne an und der Bediener der Zugprüfmaschine streicht mit dem Finger über das Blech, so ändern die DMS trotz so großer Zugkräfte die am Messgerät angezeigten Wiederstände. DMS sind folglich sehr sensible Sensoren.
Zählverfahren
Dynamische Betriebssimulation
Mit zunehmender Vernetzung technologischer Sparten wird der Ingenieurberuf immer komplexer. Um in der modernen Zeit eine optimale Werkstoffwahl zu treffen, müssen Ingenieure längst nicht mehr rein wirtschaftliche Aspekte beachten. Ökologische Kriterien wie bspw. möglichst geringe Verschwendung des Ausgangsmaterials und eingesetzer Ressourcen sind bei der Werkstoffwahl einzuhalten. Das bedeutet, dass Überdimensionieren auch bei kostengünstigem Material keine Lösung morderner Probleme darstellt.
Anforderungen an die Materialwahl steigen jedoch nicht nur aufgrund äußerlicher Einflüsse. Morderne Anlagen und Geräte müssen immer mehr leisten; so laufen viele Maschinen 24/7. Es werden höhere Maschinenlaufzeiten unter geringerem Verschleiß vorausgesetzt, sodass die Qualitätsanforderungen stetig steigen. Immer öfter wird Einsatz wiederverwendbarer Materialien erwartet.
Unter oben genannten Aspekten müssen Bauteile desweiten für eine möglichst realitätsgetreue Nutzungsart und -dauer ausgelegt werden, wobei sie in der Realtität selten rein statisch oder gleichbleibend dynamisch belastet werden.
Um einen realen Lebenszyklus möglichst anwendungsorient simulieren zu können, eignet sich die dynamische Betriebssimulation. Mithilfe von Näherungsmethoden, die die Auswertung komplexer Lebenszyklen ermöglichen, können realitätsnahe Belastungsabläufe simuliert werden. Im Rahmen des Praktikums erhalten Studierende die Möglichkeit, eine Näherung selbstständig vorzunehmen. Anschließend wird das Ergebnis am Hydropulser demonstriert.
Beschichtungsverfahren: Vergolden, Vernickeln, Brünieren
Studierende dürfen unterschiedliche metallische Proben selbstständig beschichten. Zuächst dürfen sie hierbei geeignete Verfahren zur Präparation des Materials wählen: Ultraschallbad, Zitronensäure etc..
Daraufhin werden im Praktikum die drei o. g. Beschichtungsverfahren durchgeführt.
1. Vergolden:
Das Tamponierverfahren eignet sich zum Aufbringen hauch dünner Schichten. Es dient in erster Linie der optischen Aufwertung von Bauteilen. Studierende vergolden im Praktikum Goldmünzen
2. Vernickeln:
Nickel ist beständig gegen Luft, Wasser, verdünnte Säuren und Laugen. Bauteile können galvanisch und chemisch vernickelt werden. Beide Verfahren werden den Studierenden im Rahmen des Praktikums näher gebracht. Die Studiernden lernen die Vor- und Nachteile der unterschiedlichen Verfahren kennen.
3. Brünieren:
Auch wenn das Brünieren kein Beschichtungsverfahren darstellt, wird den Studierenden das Brünieren an einem Rundstab demonstriert. Die schwarze Schutzschicht hilft dabei, Korrosionsvorgänge zu vermeiden bzw. verlangsamen.
Bruchmechanik
Belastet man einen Ideal-Kristall mit einer Kraft [F] oder einem Moment [Nm], so ergibt sich durch den entsprechenden Querschnitt eine Beanspruchung [σ], die zum sofortigen Bruch führt. Der Idealkristall bricht sofort, da er keinerlei Gitterbaufehler hat, die bei Belastung durch den Werkstoff wandern und somit Verformung(en) möglich machen.
Jede Belastung eines Werkstoffes mit Gitterbaufehlern führt zu einer Versetzungsbewegung, die aufgrund der Endlichkeit des Werkstückes auf die Oberfläche trifft und dort zunächst zu mikroskopisch kleinen Veränderungen des Gefüges bzw. zu einem sog. Mikroanriss führt. Werkstoffe “vergessen” Verformungen nicht, auch wenn die Belastungen unterhalb der Streckgrenze liegen. Tritt eine Beanspruchung nochmal auf, so wird der Mikroanriss immer größer. So wächst ein mikroskopisch kleiner Riss mit jedem Lastwechsel und vermindert dabei immer weiter den tragenden Querschnitt. Schlussendlich brechen unter diesen Gegebenheiten auch Realkristalle, wobei sie vor dem Bruche eine bestimmte Anzahl an Lastwechseln ertragen.
Demonstration des Ver- und Entfestigunsvorgangs am Hydropulser
Studierende lernen im Studium, dass Spannungen unterhalb der Streckgrenze nicht zu irreversiblen Schädigungen an Bauteilen führen. Nichtsdestotrotz versagen Bauteile in der Realität oft unterhalb Re bzw. Rp0,2. Dabei kommt es ohne jegliche Vorankündigung zum Bauteilversagen. Ein Grund dafür kann die sogenannte Alterung von Werkstoffen sein.
Die Abbildung zeigt sogenannte Hystereseschleifen, die bei dynamischen Versuchen mit dem Hydropulser im WKP-Labor aufgenommen werden können. Dabei stellen die grünen Schleifen den jeweils ersten Be- und Entlastungsvorgang einer Belastungsserie dar. Mit voranschreitender Versuchsdauer führen komplexe Vorgänge im Inneren des Bauteils zu Ver- bzw. Entfestigung des Werkstoffes. Dies wird durch die im Laufe der Zeit veränderte Hystereseschleife deutlich: im Falle einer Verfestigung entstehen blau gekennzeichnete Veränderungen der Hystereseschleife; in Fällen von Entfestigung orangene.
Durch wiederkehrende Spannungen unterhalb der Streckgrenze kommt es aufgrund komplexer Verformungsvorgänge im Inneren des Materials zu plastischen Verformungen des Prüflings. Folge davon ist ein jeweils verändertes Werkstoffverhalten. Ein zyklisch stabiles Werkstoffverhalten liegt vor, wenn nach einer bestimmten Anzahl von Lastspielen keine signifikanten Änderungen der Hystereseschleife erkennbar sind.
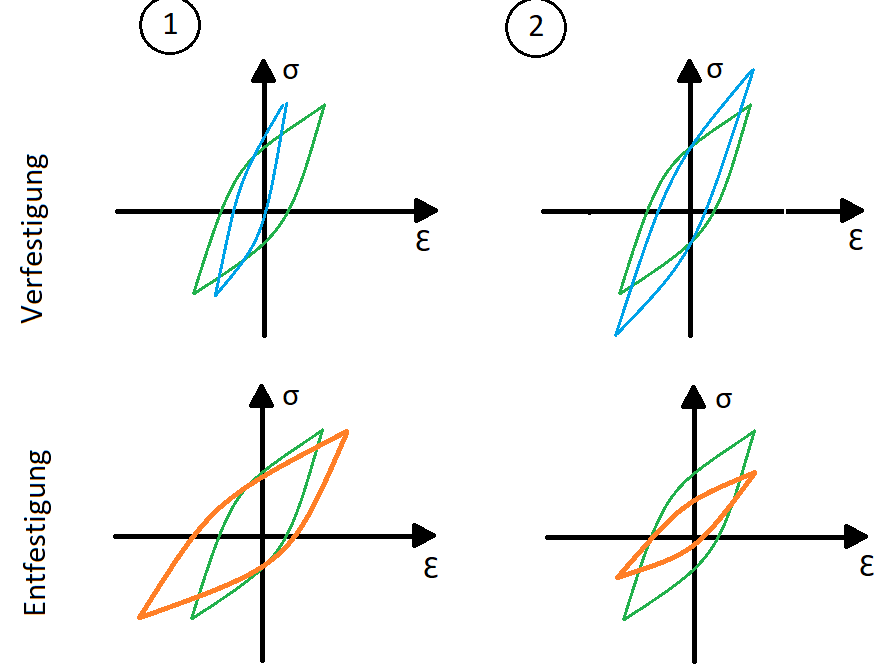
Korrosion
Korrosion bezeichnet eine durch Oxidation bewirkte Zersetzung von Metallen. Dies kann zur Beeinträchtigung der Hauptfunktion eines Bauteils bis hin zum kompletten Versagen einer ganzen Baugruppe führen. Mithilfe von Salzsprühnebeltests können Werkstoffe/ Metalle hinsichtlich ihrer Korrosionseigenschaften geprüft werden.
Einem zur regelkonformen Positionierung von Prüflingen ausreichend großen Prüfraum werden Salzlösung sowie Sprühluft zugeführt. Der Prüfraum wird mithilfe einer eingebauten Heizung auf eine vorgegebene Temperatur gebracht und die Isolierung der Kammer hilft dabei, die eingestellte Temperatur konstant zu halten. Die zugeführte Druckluft ist absolut trocken und hat keine Feuchte. Deswegen sind Beheizung, Luftverteiler und -befeuchter der Druckluft essenziell. Mithilfe des Sprudlers, des Befeuchters und der Heizung lässt sich die zunächst absolut trockene Luft gezielt und definiert anfeuchten, sodass die Versuchsparameter der Salzsprühtests individuell variiert werden können. Auch der Konzentrationsgehalt der Salzlösung stellt einen Parameter dar, der sich individualisieren lässt. So werden Metalle in salzhaltiger Nebelatmosphäre auf ihre Korrosionsbeständigkeit geprüft.